Paper:
Real-Time Inspection of Rod Straightness and Appearance by Non-Telecentric Camera Array
Leo Miyashita* and Masatoshi Ishikawa*,**
*The University of Tokyo
7-3-1 Hongo, Bunkyo-ku, Tokyo 113-8656, Japan
**Tokyo University of Science
1-3 Kagurazaka, Shinjuku-ku, Tokyo 162-8601, Japan
In this paper, we propose a measurement system that employs a camera array based on a non-telecentric optical system and an accompanying measurement algorithm to measure the straightness, length, diameter, and appearance of a rod. Measurements using telecentric optical systems, which employ orthogonal projection to preserve the dimensional ratios regardless of distance, are common in image-based inspection of the dimensional or geometrical tolerances of industrial products. However, some cases depend on the size of the target or inspection item, wherein it is difficult to configure a measurement system using telecentric optical systems. As an example, this study considers the measurement of straightness of a long rod and shows that it is possible to achieve high measurement accuracy using non-telecentric optical systems by introducing methods to calibrate miniscule errors and distortions that remain uncorrected in conventional image calibration methods. We also show that the same measurement allows for the measurement of other inspection items and evaluation of their respective measurement accuracies, thereby proving that a flexible image-based inspection process can be constructed using the proposed system and method.
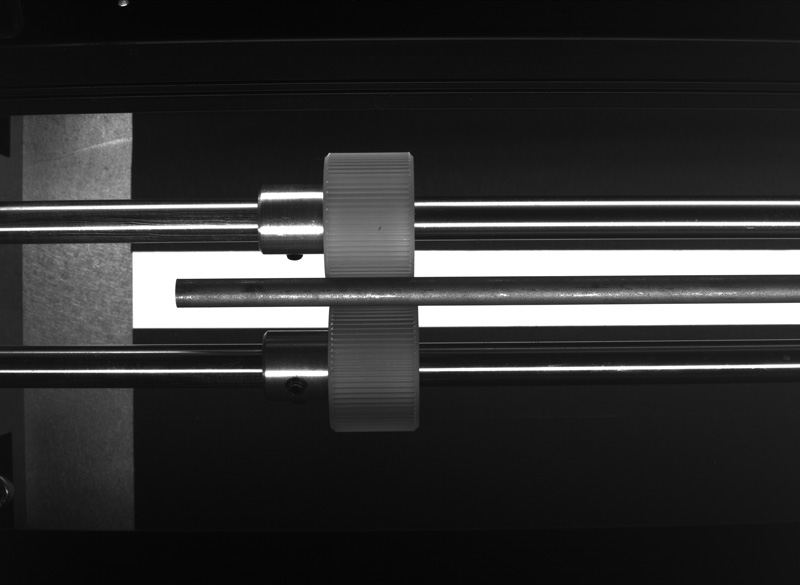
Raw image of a target rod
- [1] J. P. Yun, W. C. Shin, G. Koo, M. S. Kim, C. Lee, and S. J. Lee, “Automated defect inspection system for metal surfaces based on deep learning and data augmentation,” J. of Manufacturing Systems, Vol.55, pp. 317-324, 2020.
- [2] K. Morishita, T. Hayakawa, Y. Moko, H. Kameoka, and M. Ishikawa, “Tunnel inspection system using high-speed moving visual inspection vehicle,” Proc. of 25th ITS World Congress, AP-TP1421, 2018.
- [3] T. Hayakawa and M. Ishikawa, “Development of Motion-Blur-Compensated High-Speed Moving Visual Inspection Vehicle for Tunnels,” Int. J. Struct. Civ. Eng. Res., Vol.5, No.2, pp. 151-155, 2016.
- [4] T. Ishizawa, N. Kanamori, T. Nakamura, and M. Mizoguchi, “An Attempt to Detect Microscopic Scratches on Glossy Curved Surfaces by Camera Images,” Proc. of JSME annual Conf. on Robotics and Mechatronics (Robomec), 2A1-R01, 2019.
- [5] C. Park, S. Choi, and S. Won, “Vision-based inspection for periodic defects in steel wire rod production,” Opt. Eng., Vol.49, No.1, 017202, 2010.
- [6] B. Chen, W. Chen, and B. Pan, “High-precision video extensometer based on a simple dual field-of-view telecentric imaging system,” Measurement, Vol.166, 108209, 2020.
- [7] Y. Zhu and G. Qi, “Studies on Image Stitching Algorithms in Machine Vision Inspection of Solar Panel,” Proc. of 26th Int. Conf. on Systems Engineering (ICSEng), pp. 1-5, 2018.
- [8] S. Huang, Y. Peng, and X. Guo, “Dynamic Inspection Method of Motor Winding Defects Based on Scanning Inductive Thermography and Image Registration,” Proc. of IEEE 4th Int. Electrical and Energy Conf. (CIEEC), pp. 1-6, 2021.
- [9] R. Usamentiaga and D. F. Garcia, “Multi-camera calibration for accurate geometric measurements in industrial environments,” Measurement, Vol.134, pp. 345-358, 2019.
- [10] M. Grunwald, M. Hermann, F. Freiberg, P. Laube, and M. O. Franz, “Optical surface inspection: A novelty detection approach based on CNN-encoded texture features,” Proc. of SPIE 10752, Applications of Digital Image Processing XLI, 107521E, 2018.
- [11] S. Zhang, B. Li, F. Ren, and R. Dong, “High-Precision Measurement of Binocular Telecentric Vision System With Novel Calibration and Matching Methods,” IEEE Access, Vol.7, pp. 54682-54692, 2019.
- [12] H. Tanaka, K. Tozawa, H. Sato, M. O-hori, H. Sekiguchi, and N. Taniguchi, “Application of a New Straightness Measurement Method to Large Machine Tool,” CIRP Annals, Vol.30, Issue 1, pp. 455-459, 1981.
- [13] H. Tanaka and H. Sato, “Extensive Analysis and Development of Straightness Measurement by Sequential-Two-Points Method,” ASME. J. Eng. Ind., Vol.108, No.3, pp. 176-182, 1986.
- [14] S. Kiyono, Y. Asakawa, M. Inamoto, and O. Kamada, “A differential laser autocollimation probe for on-machine measurement,” Precision Engineering, Vol.15, Issue 2, pp. 68-76, 1993.
- [15] Q. Feng, B. Zhang, and C. Kuang, “A straightness measurement system using a single-mode fiber-coupled laser module,” Optics & Laser Technology, Vol.36, Issue 4, pp. 279-283, 2004.
- [16] Z. Zhang, “A flexible new technique for camera calibration,” IEEE Trans. on Pattern Analysis and Machine Intelligence, Vol.22, No.11, pp. 1330-1334, 2000.
- [17] A. Datta, J.-S. Kim, and T. Kanade, “Accurate camera calibration using iterative refinement of control points,” Proc. of IEEE 12th Int. Conf. on Computer Vision Workshops (ICCV Workshops), pp. 1201-1208, 2009.
- [18] D. Claus and A. W. Fitzgibbon, “A rational function lens distortion model for general cameras,” Proc. of IEEE Computer Society Conf. on Computer Vision and Pattern Recognition (CVPR’05), Vol.1, pp. 213-219, 2005.
- [19] H. Yang, Y. Chen, K. Song, and Z. Yin, “Multiscale Feature-Clustering-Based Fully Convolutional Autoencoder for Fast Accurate Visual Inspection of Texture Surface Defects,” IEEE Trans. on Automation Science and Engineering, Vol.16, No.3, pp. 1450-1467, 2019.
This article is published under a Creative Commons Attribution-NoDerivatives 4.0 Internationa License.